Modern-day printing presses are built to last and deliver high quality results.
The story of modern-day printing presses kind of starts at the beginning of the 19th century as the German engineer Friedrich Koenig, along with watchmaker Andreas Friedrich Bauer introduced a high-speed steam-powered printing press, which could print up to 1,100 sheets per hour. A far cry from Gutenberg’s press that could deliver 240 sheets per hour and the then competition Stanhope’s hand-operated press that could dish out at a speed of 480 per hour and laid the foundation on which all later printing machines were built. If the early parameter of success for a printing press was speed, now a successful press has to score high in areas of reliability, accuracy and customer fit.
Printing machines are built to last. Cleaved from solid chunks of metal and essentially built like brick outhouses, offset printing presses act as sturdy workhorses going about completing all manners of their daily tasks with absolute reliability. It is a given, that in the long run, only well-tried machines which are fully capable of standing up to hard work and which have been built as rationally as possible. The usefulness of such a machine is measured by its productive performance i. e. in both quality and quantity, by its ease of operation and by its reliability and potential service life. The expert user of today demands a positive experience at all times and under all conditions. Notwithstanding the sophistication, the main job of the machine is still in addition to functioning correctly, to stand up to the highest strains and stresses likely to be imposed during printing.
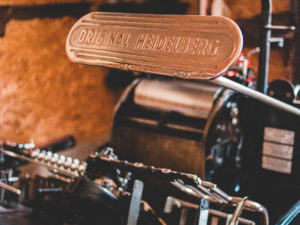
The evolutionary trajectory of the printing press has been complicated, but at every level, it has enhanced accuracy. The many new and interesting types now available to users could only be designed after a large number of complicated printing and production problems had been solved. All the knowledge gained along was applied to make vast improvements in machine engineering and designing of printing machines. A lot is owed to the intensely competitive machine designing eco-system. The innovation race between the various printing processes in a way was most necessary and essential to attain the high degree of perfection reached by many modern machines.
By design, industrial printers have to carry a heavy load. Besides having the muscle to run continuously for long hours, the expectation is that they produce premium quality. The quality of delivery has been brought to a state of excellence and has been even further improved by the addition of new accessories. The printers of today value the speed and economy aspect of operating machines which, apart from saving space, are attractive in appearance and can also display task execution flexibility- which can be used for non-stop printing of all kinds. The printer’s main job, after procuring such a machine, is simply to ensure that idle and non-productive times are cut down to a minimum.
The process of delivering quality service has always been, without exceptions the direct result of harmoniously combining the four variable factors viz printing block or form, ink or colour, the material on which the print is made (normally this is paper) machine and printer. The vital role of the printer is to ensure that each and every one of these individual components harmonises optimally with the others. To maintain harmony, the additional aspect of maintenance is critical. The user also demands a stronger than earlier printing system which is easily accessible for repair or assembly purposes.
Modern-day printing presses high performance both qualitatively and quantitively and the extreme economy of the whole printing process have fuelled the rise of a vibrant and versatile global industry.
Visit the Machine Dalal website or simply download our app onto your Android or iOS smartphone.