Digital twin technology is widely adopted across various sectors, enabling industries, particularly production enterprises, to enhance their technological capabilities. This technology leverages physical models to construct 3D digital replicas of real-world production line data. It facilitates online management and control of physical entities through their virtual counterparts, bridging the gap between physical operations and digital monitoring.
Introduction
The printing industry plays a vital role in the national economy, serving as a key component and supporting industry. However, in recent years, it has faced challenges due to environmental regulations and other related policies. In contrast to traditional book printing, the flexible packaging sector has maintained a more favorable growth trajectory. Notably, the gravure flexible packaging printing industry has made significant strides despite considerable market and environmental pressures.
Historically, the traditional manufacturing sector has been characterized by labor-intensive practices and high energy consumption. However, with advancements in technology and production capacity, there is a growing trend towards integrating manufacturing with information technology. Initiatives such as Germany’s “Industry 4.0” and China’s “Made in China 2025” emphasize the importance of the Internet of Things (IoT), intelligent simulation, and industrial big data.

Shaping the Industry 4.0 ecosystem needs to focus on the combination of various technologies and resources. Digital twin technology can realize the precise mapping relationship between physical entities and their digital virtual entities. By incorporating physical entity simulation models and industrial production parameters into virtual models, companies can achieve functionalities such as:
- Three-Dimensional Monitoring: Real-time tracking of production processes.
- Remote Operation and Maintenance: Managing operations from a distance.
- Production Guidance: Assisting operators in optimizing workflows.
- Predictive Maintenance: Anticipating equipment failures before they occur.
- Product Redesign: Innovating packaging solutions based on performance data.
For flexible packaging printing companies, applying digital twin technology can lead to improved labor cost efficiency, enhanced production quality tracking, and overall increased productivity.
Understanding Digital Twin Technology
A digital twin refers to the comprehensive utilization of physical models, sensor updates, operational history, and other relevant data to create a virtual representation that reflects the entire lifecycle of corresponding physical equipment. This involves multi-disciplinary simulations across various scales and probabilities.
Programming Concepts
Digital twins employ two primary programming concepts:
Object-Oriented Programming: This approach encapsulates real-world objects as “classes” within the software, defining their attributes and functions.
Process-Oriented Programming: This method focuses on executing steps in a sequence based on real-world events, allowing for hierarchical relationships that describe causal connections over time.
For flexible packaging printing companies that experience discrete production changes, adopting process-oriented thinking is particularly beneficial for tracking the entire lifecycle of production processes.
The Conceptual Evolution of Digital Twins
Initially termed the “information mirror model,” digital twins represent a blend of physical and virtual worlds. As the name implies, the real world is formed into a three-dimensional information body through virtual technology to realize the non-contact perception of real things. A pattern in which the physical world in the physical dimension and the virtual world in the information dimension coexist and blend together. As an emerging and rapidly developing technology, digital twins provide a new direction for advancing the whole process perception and high-quality production of flexible packaging production.
Applications of Digital Twin Technology in Flexible Packaging Production
Information Communication in Workshops

Better communications
The long-term nature of production processes generates vast amounts of data communication and storage requirements. This includes not only information about production processes but also equipment operating conditions and environmental parameters. While many companies have begun utilizing Manufacturing Execution Systems (MES) or Enterprise Resource Planning (ERP) systems for management purposes, challenges remain:
- Many organizations rely on single systems for production management.
- A limited number utilize multiple systems without effective data sharing between them.
Modern digital twin workshops necessitate unified management of all workshop information and data through an integrated decision-making system that encompasses order processing, equipment status monitoring, and environmental testing parameters.
Composition of Flexible Packaging Production Lines
Traditional flexible packaging workshops typically consist of several key areas:
- Raw Material Workshop
- Printing Workshop
- Laminating Workshop
- Curing Workshop
- Slitting Workshop
- Post-Press Processing Workshop
- Transfer Workshop
- Finished Product Workshop
Transitioning to Digital Twin Production Lines
To implement digital twin technology effectively within traditional production lines, several adaptation technologies must be integrated. For example:
- Modeling Software: This software can facilitate comprehensive simulations of the production environment.
- Simulation Models: These models must accurately represent both physical dimensions and key machine actions to ensure high-quality monitoring throughout all elements of the production line.
Advantages of Digital Twins in Flexible Packaging Production Workshops
Integrating digital twin concepts into management practices can significantly enhance decision-making capabilities related to operations and maintenance solutions:
3D Visualization Solutions: The virtual environment allows seamless integration with real-world production processes.
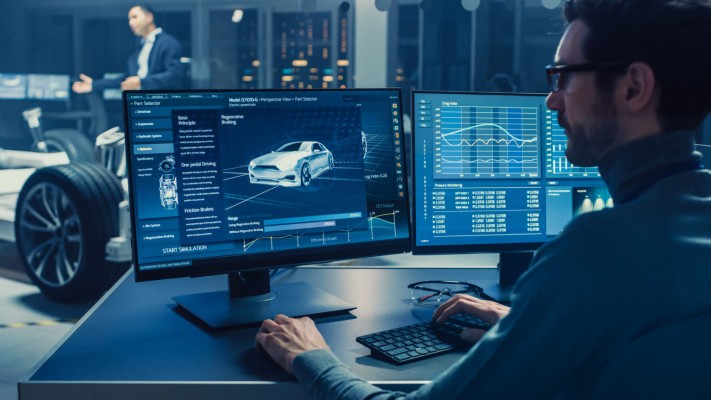
Better R&D
Better R&D.: Improvements in your R&D processes, thanks to the valuable insights Digital Twins pull from customers, processes, mechanisms, and connections received and then embedded in the models.
Simulated Production Processes: Companies can monitor risks associated with production while enabling remote collaboration.
Comprehensive Database Support: Digital twins provide robust analytical capabilities that guide enterprise development based on historical data trends.
By utilizing historical data for predictive analysis, businesses can optimize their production strategies effectively.
Future Ahead
Digital twin technology presents exciting prospects for enhancing productivity within flexible packaging manufacturing. As one of the key sectors within discrete manufacturing industries, flexible packaging still faces challenges in fully realizing the potential benefits offered by digital twins. According to expert insights, the development of digital twin technology can be categorized into three stages:
Virtual-Real Connection: Establishing initial connections between virtual models and real-world entities.
Virtual-Real Fusion: Achieving deeper integration between physical processes and their digital representations.
Virtual-Real Symbiosis: Realizing a seamless coexistence where both worlds operate harmoniously.
Flexible packaging printing companies can implement these stages progressively—from automating production adjustments to achieving real-time monitoring and ultimately perfecting virtual simulation controls.
Final Word
The digital twin technology is a perfect fusion of multiple complex technologies. There are still many obstacles in the process of practice, and it needs to be explored continuously. The application of digital twin technology is long-term research, which requires continuous refinement of the model and continuous optimization in combination with practice.
Machine Dalal platform is preferred by buyers and sellers from the global print industry to get directly connected with each other and trade their machinery.
Visit the Machine Dalal website or simply download our app onto your Android or iOS smartphone.